Aktivkohleproduktion aus Altreifen und polymeren Abfällen
Präsentation des Prozesses der Aktivkohleherstellung
Mit der Anlage AKA II
Aktivkohle und die Anwendungsbereiche
Aktivkohle ist ein poröser und feinporiger Kohlenstoff mit einer sehr großen,
inneren Oberfläche und dient in der Industrie als Basis für eine Vielzahl von
Anwendungen. Die Poren sind wie bei einem Bimsstein miteinander verbunden.
Die Oberfläche beträgt zwischen 300 und 1800 Quadratmeter pro Gramm.
Industriefilter
Das Material aus der Anlage ist aufgrund der Lochstruktur und der großen Oberfläche optimal für den Industriebereich geeignet. Da es nicht gepresst werden muss und sehr feinporig ist, eignet sich die Aktivkohle perfekt für alle Arten von Luftfilteranlagen, Innenfilter und Aktivkohlefiltern.
Farbindustrie
Als Pigmente für Farben und Lacke ist die Aktivkohle unerlässlich. Da die Aktivkohle nicht behandelt werden muss, ist der Aufwand der Produktion deutlich geringer.
Gummiindustrie
Bei der Produktion von Gummi wird die Aktivkohle als Füllstoff verwendet und wird als Feinpulver in der Gummiproduktion eingeknetet. Die anfallenden Abfälle aus der Gummiproduktion können dem Produktionsprozess erneut zugeführt werden und die Ressourcen aus Altreifen können vollständig und nachhaltig rückgewonnen werden.
weitere Anwendungsbereiche
Für den Medizinbereich können verschiedene Rohstoffe wie Bambus oder Naturhölzer in der Anlage verarbeitet werden. Durch die hohe Qualität der Aktivkohle sind die Anwendungsbereiche nahezu unbegrenzt.
Anlage
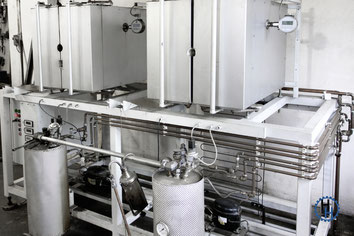
Die Anlage AKA II dient zur Vorführung des Prozesses und hat ein Fassungsvermögen von 4 kg je Retorte. Betrieben wird die Anlage mit Strom.

Der Prozess und das Verfahren sind patentrechtlich weltweit abgesichert.
Die Vorteile des Aktivkohleherstellungsverfahrens
MIT DER ANLAGE AKA II:
- Produktion von Aktivkohle mit außergewöhnlich hoher Qualität (Preis/Leistung)
- Verarbeitung von Altreifen und Abfällen aus der Gummiproduktion
- Vollständige und nachhaltige Ressourcenrückgewinnung ohne Rückstände
- Durch dieses neue Verfahren lässt sich eine Vielzahl von Arbeitsschritten einsparen und unterscheidet sich somit von den herkömmlichen Verfahren:
- Temperaturen sind deutlich niedriger, dadurch wird die Sinterung mit der Aktivkohle verhindert und der Energiebedarf ist geringer.
- Öfen werden nicht mit Gas geflutet.
- Säure- und Aufbereitungsbecken werden nicht benötigt.
- Metallgewebe ist unbeschädigt und kann im Rüttelsieb mit sehr geringem Aufwand entfernt werden.
- Die Oberfläche ist sehr hoch, da grobe Stücke sehr offenporig sind und produktionsbedingt nicht in Form gepresst werden müssen.
Aktivkohleproduktion
Für die Produktion der Aktivkohle werden grundsätzlich Altreifen und Polymere Abfälle aus der Gummiproduktion eingesetzt. Dadurch ist eine außergewöhnlich hohe Qualität des Endprodukts gewährleistet, da schon das Ausgangsmaterial qualitativ sehr hochwertig ist.
So ist es für die Gummiproduktion möglich, den angefallenen Abfall durch den Umwandlungsprozess als hochwertigen Rohstoff erneut in den Produktionskreislauf zu integrieren oder gewinnbringend weiterzuverkaufen. Durch den geschlossenen Produktionskreislauf ist der Prozess emissionsarm. Die Umwelt wird nicht belastet. Alle Gase, Öle, Kohlenstoffe, Metalle und die für den Prozess benötigte Wärme können erneut verwendet werden. Den Unternehmen bleiben teure Entsorgungskosten erspart. Bei der Ressourcenrückgewinnung von Autoreifen ist das Ausgangsmaterial (die abgefahrenen Reifen) in großen Mengen und weltweit verfügbar.
Prozess und Ablauf
Der Prozess der Aktivkohleherstellung ist eine thermische Behandlung, die einen Entgasungsprozess in die Wege leitet.
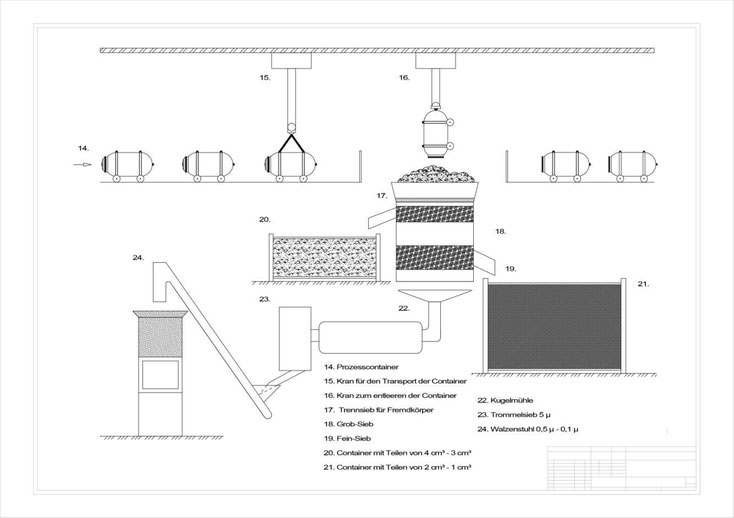
1. GEEIGNETES ROHMATERIAL ZUFÜHREN
Das Rohmaterial wird eingesammelt und in die Container - auch Retorten genannt - eingefüllt. Die speziell angefertigten Retorten ermöglichen einen sicheren Ablauf der einzelnen Prozesse.
2. AUFHEIZEN DER RETORTE
Die mobile Retorten wird der aufgeheizten Ofenanlage zugeführt und das Entgasungssystem wird angeschlossen. Die Arbeitstemperatur beträgt zwischen 300 °C bis 500 °C. Durch die mobilen Retorte muss die Temperatur des Ofens nicht hoch- und heruntergefahren werden und spart so Energie ein.
3. EXTRAKTION DER SEKUNDÄREN ROHSTOFFE
Der drucklose Entgasungsprozess findet in einem geschlossenen Kreislauf statt. Es entstehen Gas und ein schwefelhaltiges Öl, welche separat aufgefangen werden. Sauerstoff oder Stickstoff zum Fluten der Retorte werden nicht benötigt. Der sensorgesteuerte Prozess endet nach der vollständigen Entgasung des Materials.
4. WÄRMERÜCKGEWINNUNG AUS DER RETORTE
Um einen Großteil der Wärme zurückzugewinnen, wird die Retorte in die Wärmerückgewinnungskammer befördert.
5. ENTNAHME DES PRIMÄREN ROHSTOFFS
Nach der Entgasung und Abkühlung der Retorte befinden sich die hochwertige Aktivkohle und gegebenenfalls Stahlgewebe im Inneren. Die Aktivkohle wurde nachweislich durch einen Gaschromatographen auf Reststoffe untersucht und ist zur Weiterverarbeitung freigegeben.
6. WEITERVERARBEITUNG DER AKTIVKOHLE
Nach der Trennung der Fremdkörper kann die hochwertige Aktivkohle mit folgenden Schritten in mehreren Grundstufen für die Industrie aufgearbeitet werden.
Die Fremdkörper wie Stahlgewebe werden über ein Magnetband entfernt.
Die Aktivkohle wird über ein Stufenrüttelsieb nach der Größe getrennt:
- Grob-Sieb – Container mit Teilen von 3 cm³ - 4 cm³
- Fein-Sieb – Container mit Teilen von 1 cm³ - 2 cm³
- Kugelmühle – Der Mahlvorgang wird nach Kundenwunsch durchgeführt und wird an den Bedarf der Einsatzzwecke angepasst.
- Kleinste realisierbare Größen:
- Trommelsieb – bis 5 μ
- Walzenstuhl – 0,5 μ - 0,1 μ